FACILITIES AND SERVICES
Wam Metals has world-class facilities to manufacture forgings, machined and assembly products. All of our processes are controlled using the ISO 9001 Quality Management System and are audited on a regular basis.Tool-Room
Our Tool-room uses the latest machining equipment and software to design and develop new products; after which they manufacture high-quality tools, dies, clipping tools, injection moulds and machining fixtures/jigs to be used for the manufacture of products. Damaged or worn tools, dies, clipping tools and machining fixtures/jigs are also repaired and refurbished in the Tool-room.
Solidworks (3D software) | Design and edit 3D models used for manufacturing of tools, dies and jigs. |
Mastercam (3D software) | Design and edit 3D models used for manufacturing of tools, dies and jigs. |
Deckel Maho 70V | Manufacture and repair tools, dies and jigs. |
Tongtai Machining Centre | Manufacture and repair tools, dies and jigs. |
Spark Eroder | Create complex shapes tools, dies and jigs. |
Surface grinder | Prepare tools, dies and jigs before manufacture or repair. |
Lathes and milling machines | Manufacture and repair tools, dies and jigs. |
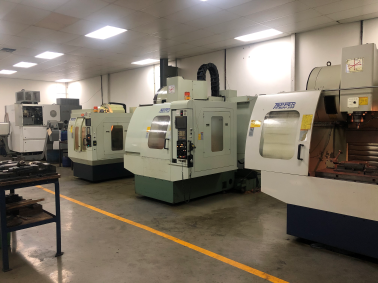
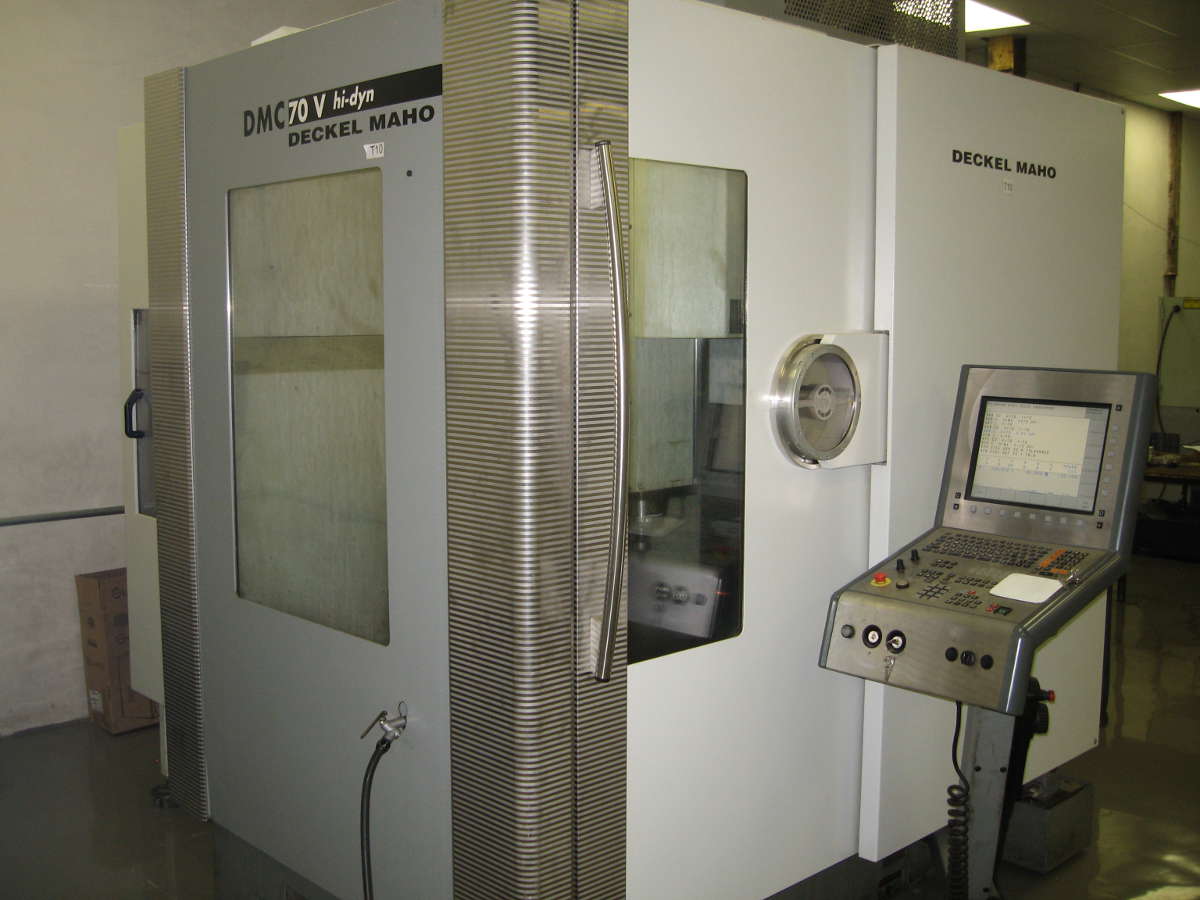
Forging, saws and clipping
The saws cut material to the correct length for forging (or machining). The cut billets are formed into various shapes and sizes using the forging presses; clipping presses then remove any excess material.
5 Band saws | Cut material to length. |
2 CNC saws | Cut material to length. |
23 Forging presses (90-530 ton) | Manufacture forgings (hot-forging and cold-forging) in various shapes/sizes. |
Forge-shop with 23 forging presses
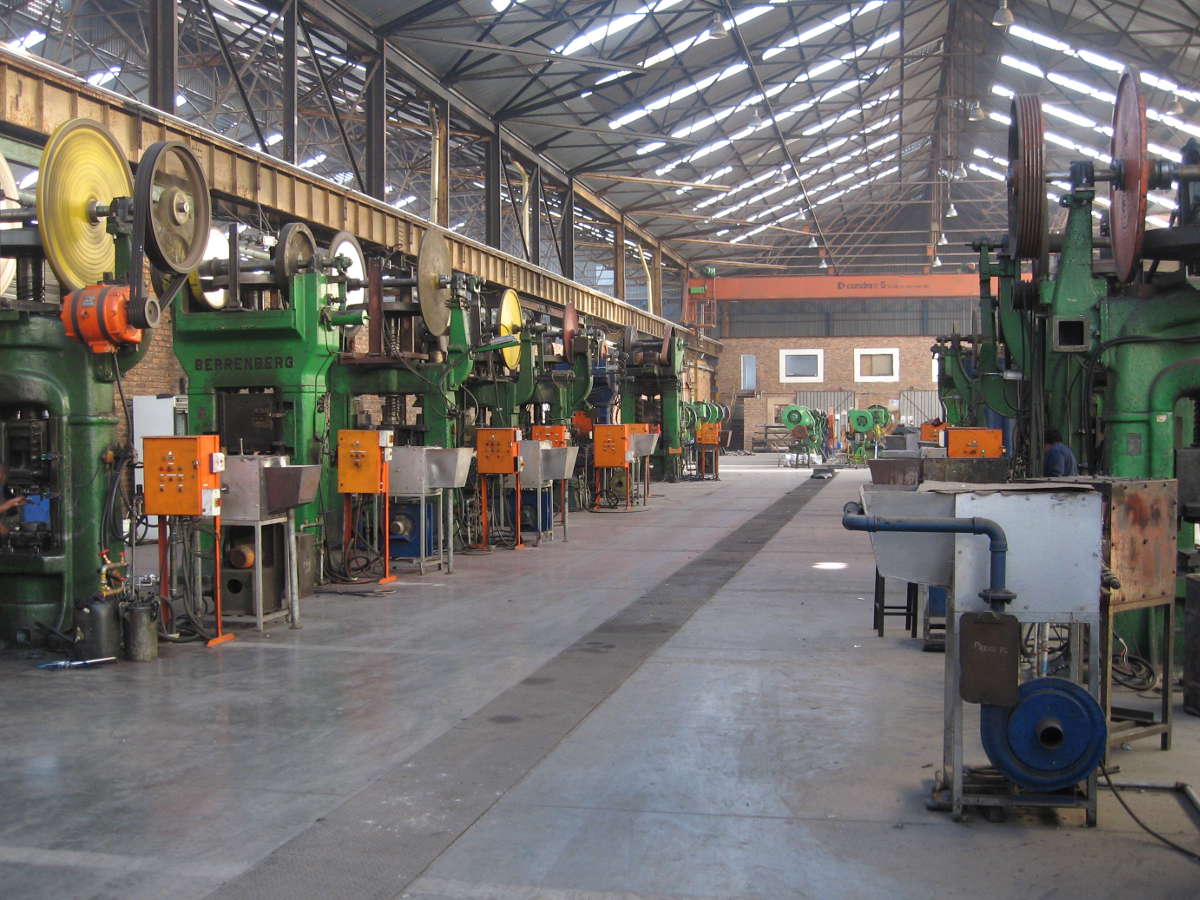
Saw cutting process
Finishing
We offer a range of finishing options (including multiple finishing) depending on the product application and customer requirements.
Fettling/linishing | Excess material is removed after forging. |
Acid dipping | Dipped in acid for a smooth, clean finish. |
Shot-blasting | Fine satin shot-blasted finish. |
Polishing | Polished to a shine. |
Electro-plating | Nickel, tin and silver plating. |
Hot dip galvanising | A zinc coating to protect iron, steel or aluminium from corrosion. |
Powder coating | Tough paint covering to protect products. |
Plating plant | Tin and nickel plating . |
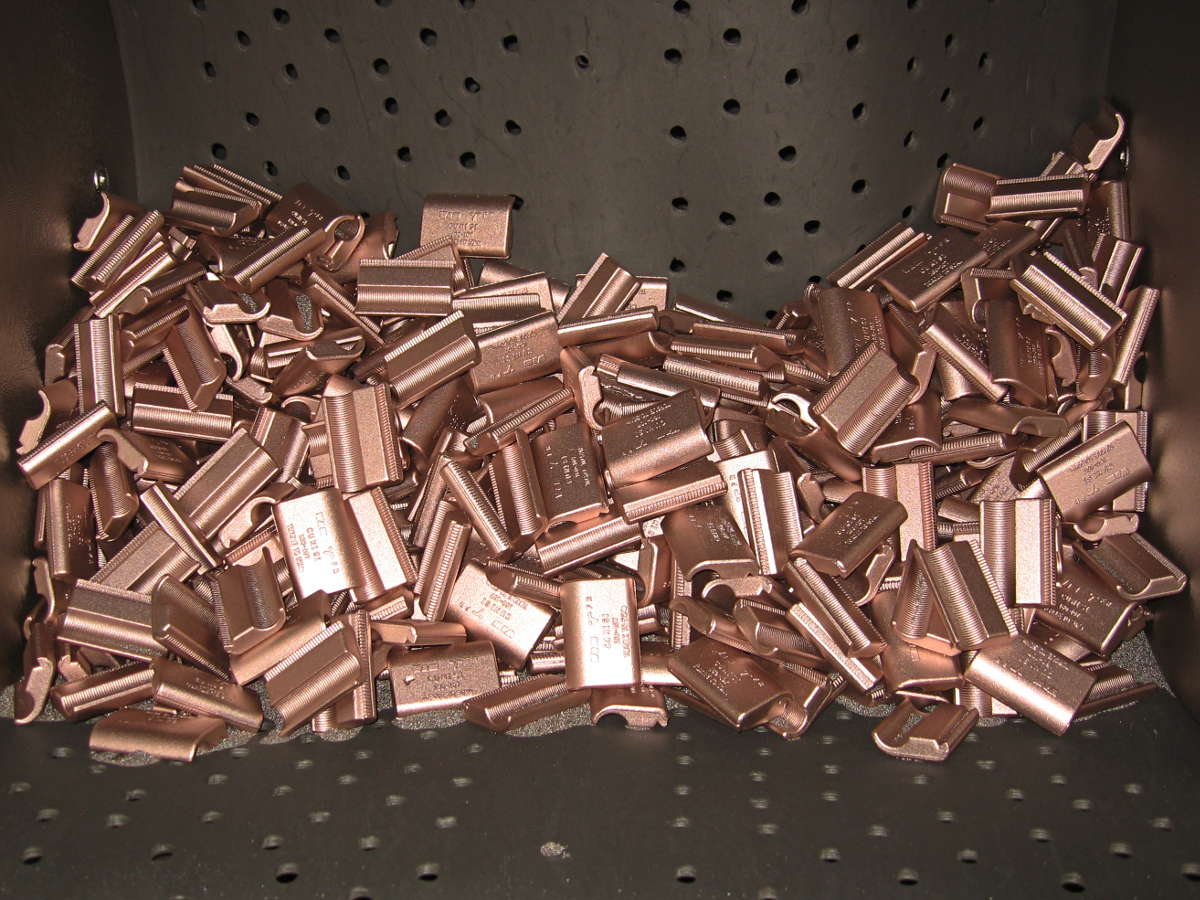
Machining
Our Machine-shop precisely machines each product to specification. All products are inspected to ensure conformity.
16 CNC Lathes | Machining of products. |
10 CNC Machining Centres | Machining of products. |
3 Special purpose machines | Machining of products. |
Drilling and tapping | Drilling holes and tapping threads. |
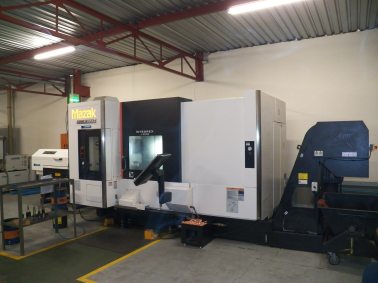
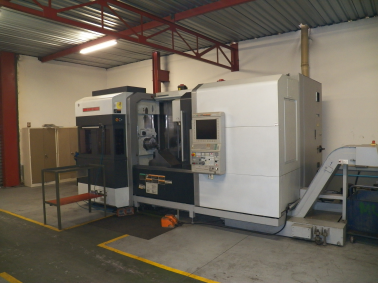
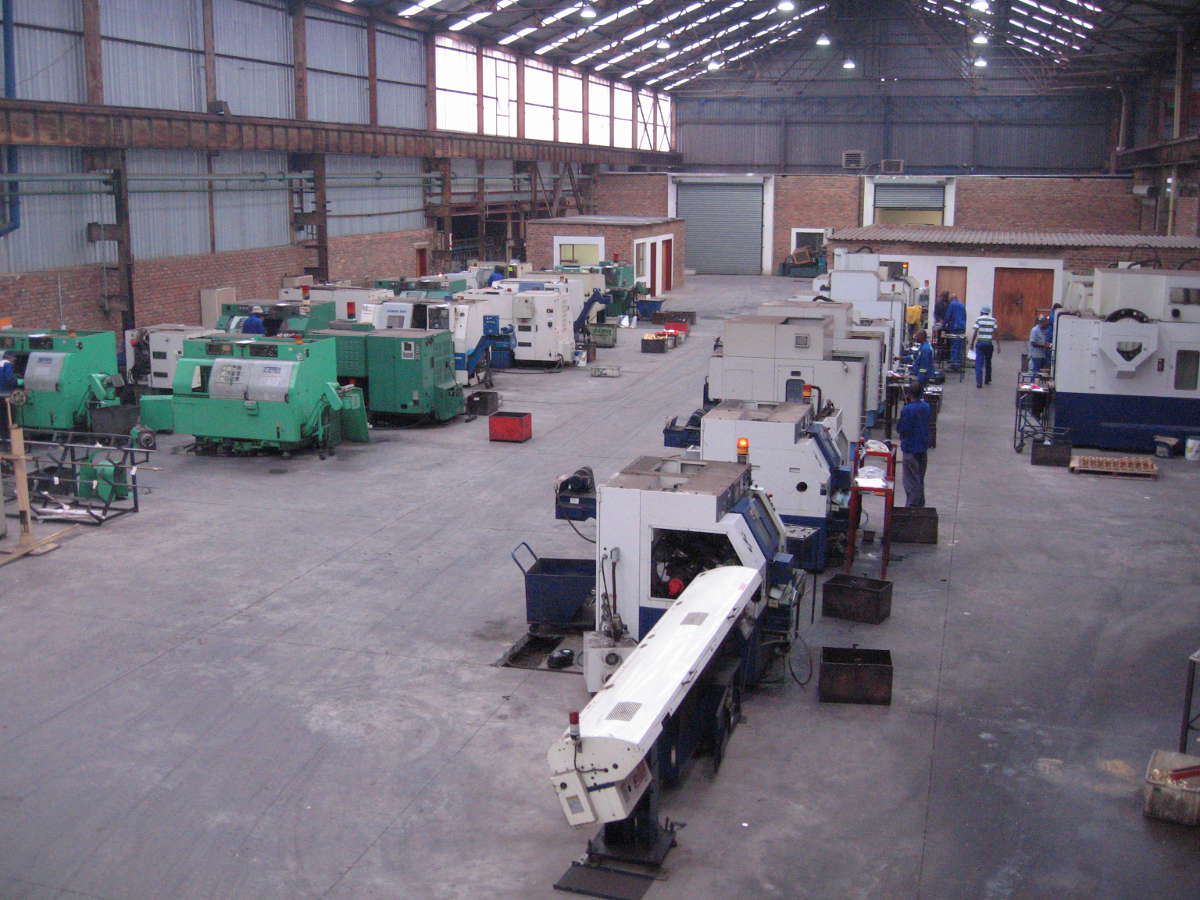
Plastic Injection moulding
Our plastic injection plant manufactures plastic parts from all injection-mouldable plastics.
Demag Injection Moulding Machines | 175 ton, 240 ton, 420 ton injection moulding machines. |
CLF Injection Moulding Machine | 125 ton injection moulding machines. |
DR Boy | 30 ton and 50 ton injection moulding machines. |
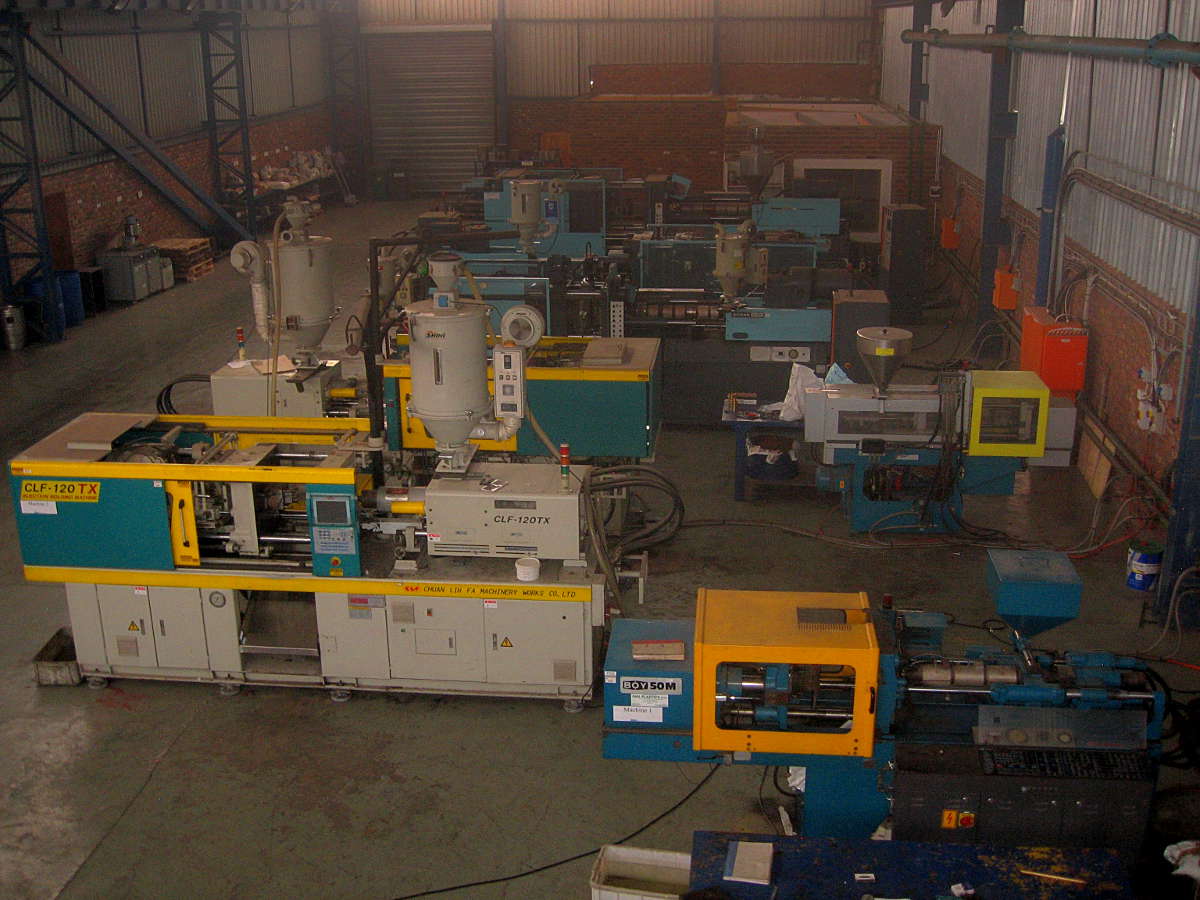